Most people are familiar with what a circuit board is along with traditional through-hole electronic components, and some people still automatically equate circuit boards with the placing of electronic components using wire leads and holes in the board. This is an older method of producing electronic components and circuit boards, and is rapidly being replaced with surface mount technology. While it may seem that SMT technology has only been around a short while, it would interest most people to know that surface mount technology has already been in use for the last twenty-five years.
Also known as SMT, surface mount technology places electronic components and fixes directly onto the circuit boards. Advances in technology have meant that SMT now allows for smaller board level components and consequently, smaller end products. Think of the size difference in early mobile phones and today's tiny cell phones, for example.
Soldering Supplies
Surface mount components can be soldered using two basic techniques - using a soldering iron or using an oven. Though the process is fairly easy, it requires care and a stable hand specially when using a soldering iron. The process starts with applying a thin layer of solder paste, which is a sticky mixture of tiny solder particles and flux, to the SMT pads which are present on the PCB and are used to hold the SMT components. Then the component is placed on the pads and carefully aligned. Next, using a clean solder iron or the oven, the component needs to be tacked into place properly by soldering two opposite pins. Once in place, the alignment is rechecked and the soldering completed.
The SMT method of mounting has a number of main advantages over older methods, allowing as it does for the placement of components in exact positions on both sides of a circuit board, reducing costs and reducing size at the same time. Though cost reductions have only come over time, the initially cost of creating the machines and designs needed to undertake surface mounting are higher than the old through-hole based mounting.
Many people still suggest that the older methods of mounting components are easier to repair, but as SMT has developed enough, along with advances in the repair tools, the methods and costs of repairing surface mount boards has fallen. While it is still possible to undertake manual soldering repairs, there have been professional rework systems designed as well which have improved the method and cost of repairs.
Surface mount components now range into three main categories, Passive SMDs (including resistors and capacitors), Transistors and Integrated Circuits. There are currently still some electronic components that require the old drilled through and lead wire methods, but the numbers are on a dramatic decline.
Look for further advances in surface mount technology in the coming years. As the technology improves, the electronic components will get smaller and smaller. Learning how to use them now will keep you on top of the industry.
Special Price!!! Weller 8125N Replacement Soldering Gun Tip with Hex Nut
Click for larger image and other views
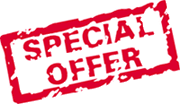
Weller 8125N Replacement Soldering Gun Tip with Hex Nut Feature
- Returns will not be honored on this closeout item
Weller 8125N Replacement Soldering Gun Tip with Hex Nut Overview
WELLER PREMIUM SOLDERING IRON REPLACEMENT TIP *Tin plated tip *Includes tip nuts *For Weller Mfg. No. 8200 soldering gunSAVE NOW on the special offers below!
Available In Stock. |
This Weller 8125N Replacement Soldering Gun Tip with Hex Nut ships for FREE with Super Saver Shipping. |
Price : Click to Check Update Prices Please. |
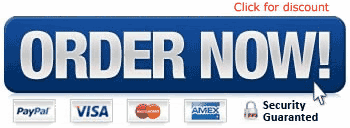